Pressure Process Trainer
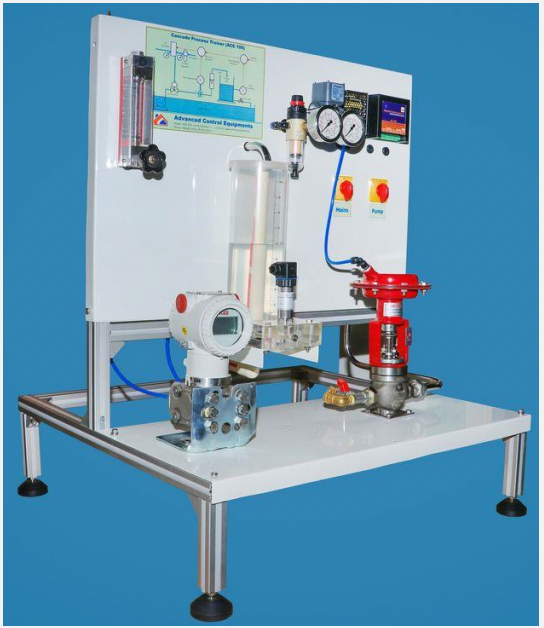
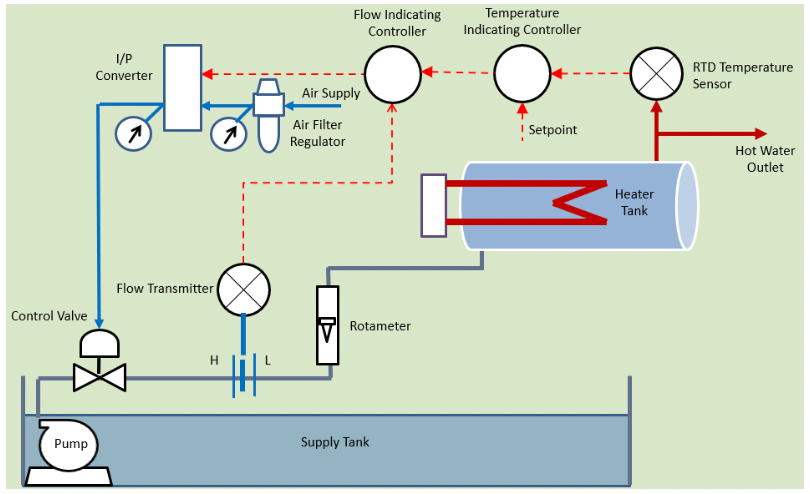
Description
The Cascade Process Trainer is designed to understand the elements of a cascade process technique and its control. It consists of two loops namely the flow loop (Inner or Slave loop) and the level loop (Outer or Master loop). The output of the primary (Level) loop will go as the setpoint of the secondary (Flow) loop. The setup is designed to perform Level, Flow and Cascade experiments. The setup consists of a process tank fitted with a level transmitter, an orifice to measure flow with a differential pressure transmitter and necessary drain valve arrangements. The inlet flow to the process tank is controlled by a control valve which operates on a 3 to 15 psi pressure signal. A current to pressure (I/P) converter is used to convert the output of the controller (4-20mA) to the signal pressure. The process parameters are controlled by a programmable logic controller. These units along with necessary piping are fitted on the support frame. The setup is designed for tabletop placement and access. The controller is connected to computer through USB for monitoring and controlling the process. User friendly software will be supplied along with the hardware to perform different set of experiments.
Features
- Open loop / Closed loop operation
- Stability analysis
- On/Off, P, PI, PD and PID control mode
- MODBUS communication
- Open / closed loop / Auto tuning
- Empirical model Estimation
- User friendly GUI
- Single click data log, export features
Range of Experiments
Level, Flow measurement and transmitter
characteristics studyStudy of I/P Converter
Open Loop Analysis
Study of On/Off Control & Hysteresis
Study of P Mode & Bias
Study of PI Mode
Study of PD Mode
Study of PID Mode
Empirical Model Estimation
ZN Closed loop PID Tuning
ZN Open loop PID Tuning
Stability Analysis
Study of Cascade Control
Product Specifications
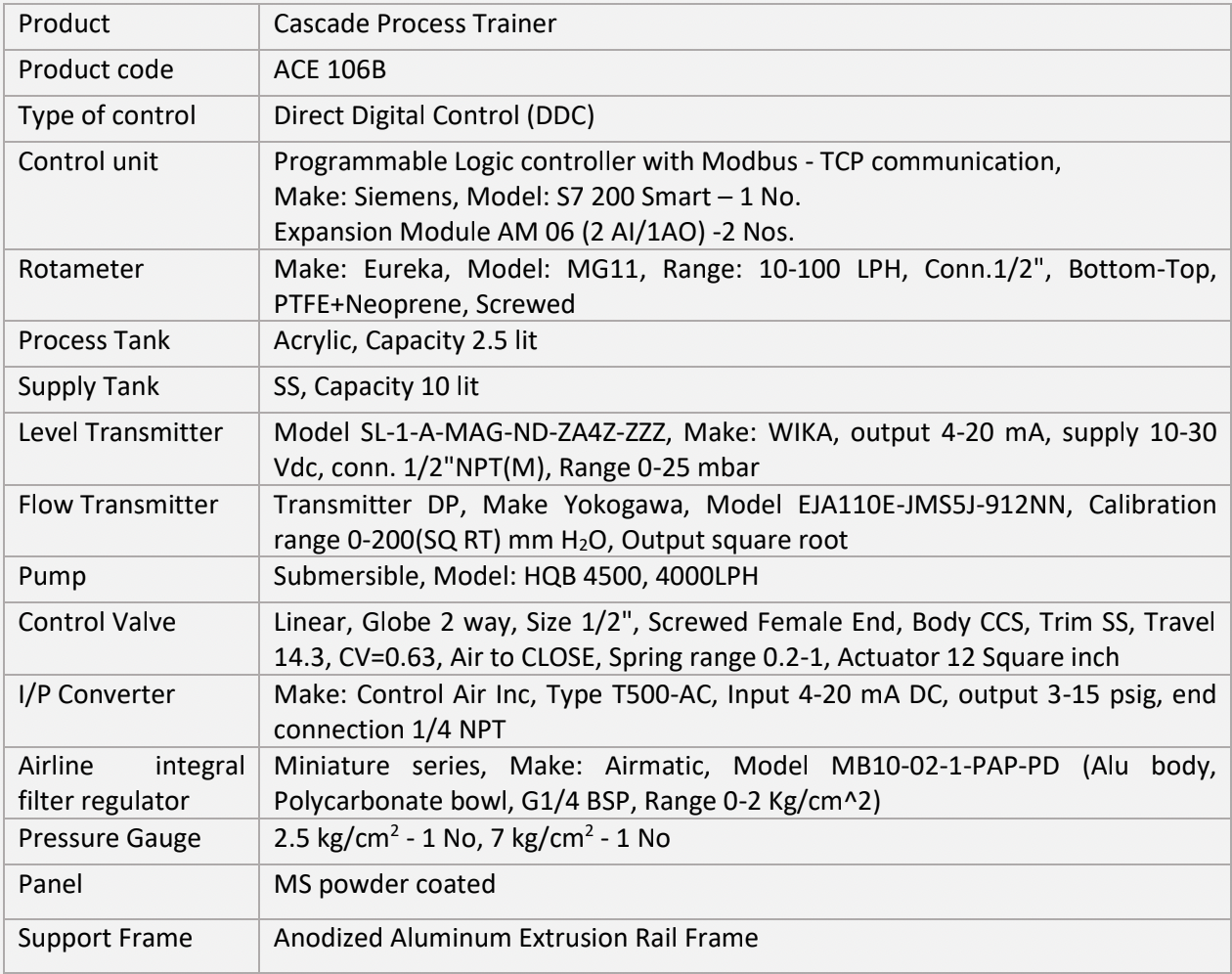
List of Experiments & Components
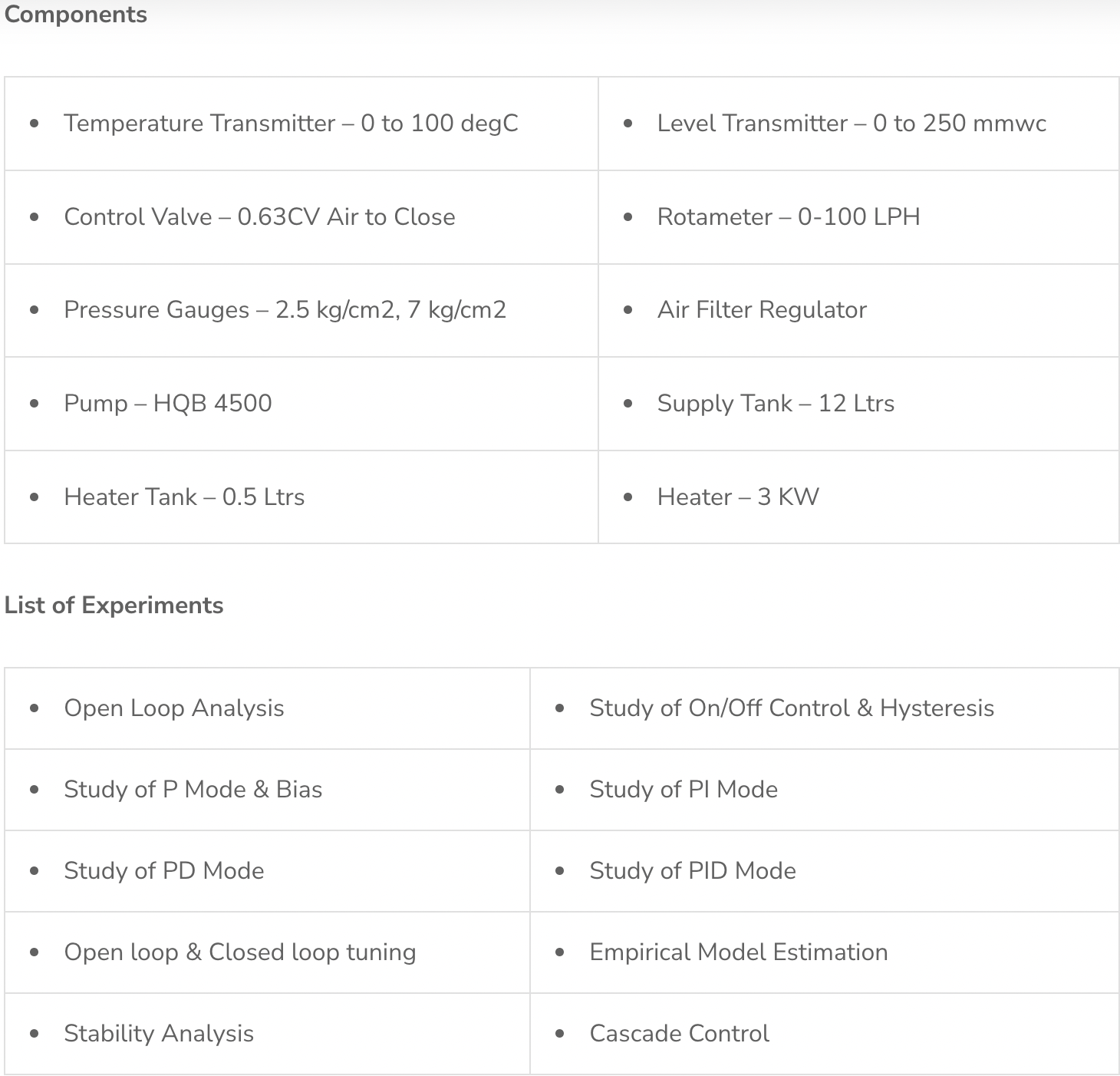