Pressure Process Trainer
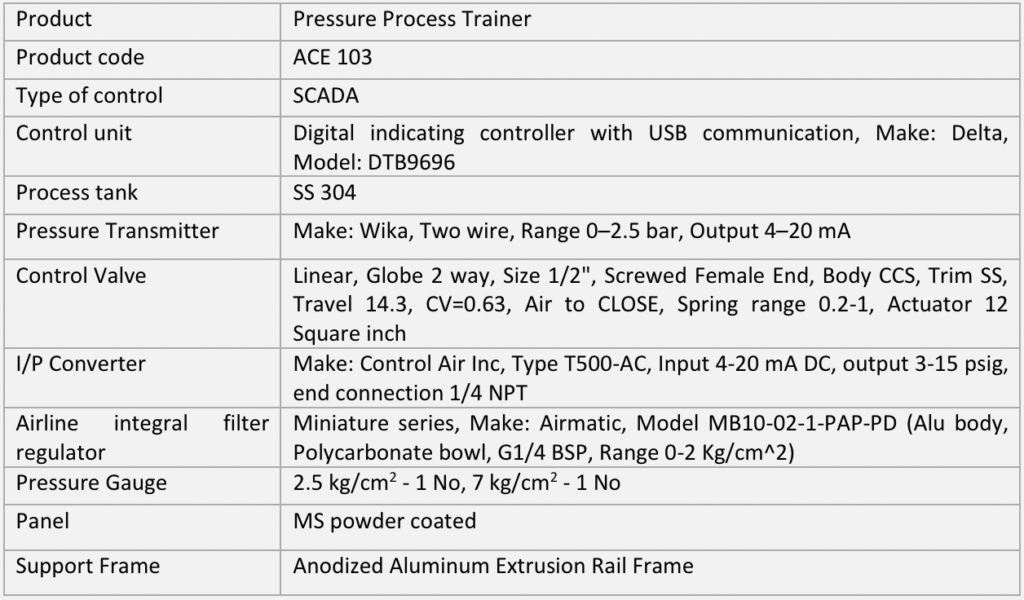
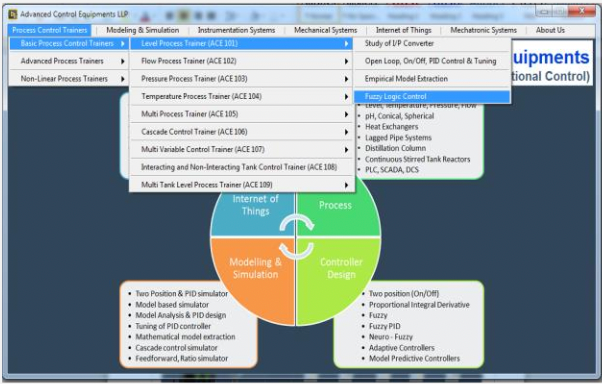
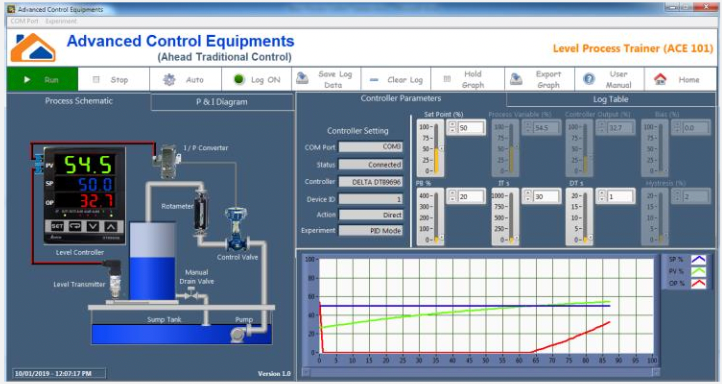
Description
The Pressure Process Trainer is specifically designed to facilitate the understanding of pressure processes and their control. It comprises a pressure process tank and a pressure transmitter. The tank features an inlet pipe line, which connects to the compressor or pressure supply, as well as an outlet pipe line and a vent pipe line. The outflow is regulated by a control valve, which operates on a 3 to 15 psi pressure signal. To convert the output of the controller (4-20mA) to the signal pressure, a current to pressure (I/P) converter is employed. The process parameter is controlled by a digital indicating controller. These components, along with necessary piping, are mounted on a support frame, making the setup suitable for tabletop placement and access. Furthermore, the controller is connected to a computer via USB for monitoring and controlling the process. User-friendly software will be provided along with the hardware to conduct various sets of experiments.
Features
- Open loop / Closed loop operation
- Stability analysis
- On/Off, P, PI, PD and PID control mode
- MODBUS communication
- Open / closed loop / Auto tuning
- Empirical model Estimation
- User friendly GUI
- Single click data log, export features
Range of Experiments
- Pressure measurement and transmitter characteristics study
- Study of I/P Converter
- Open Loop Analysis
- Study of On/Off Control & Hysteresis
- Study of P Mode & Bias
- Study of PI Mode
- Study of PD Mode
- Study of PID Mode
- Empirical Model Estimation
- ZN Closed loop PID Tuning
- ZN Open loop PID Tuning
- Stability Analysis
- Auto Tuning
Product Specifications
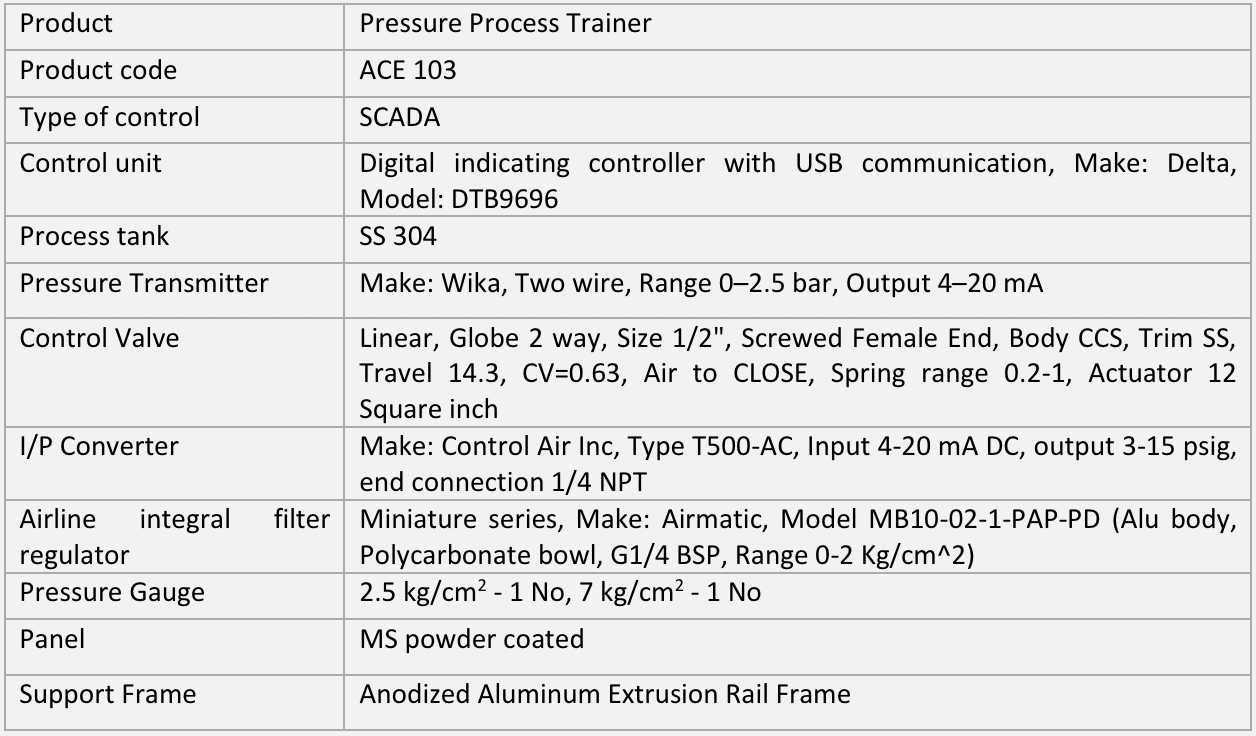
List of Experiments & Components
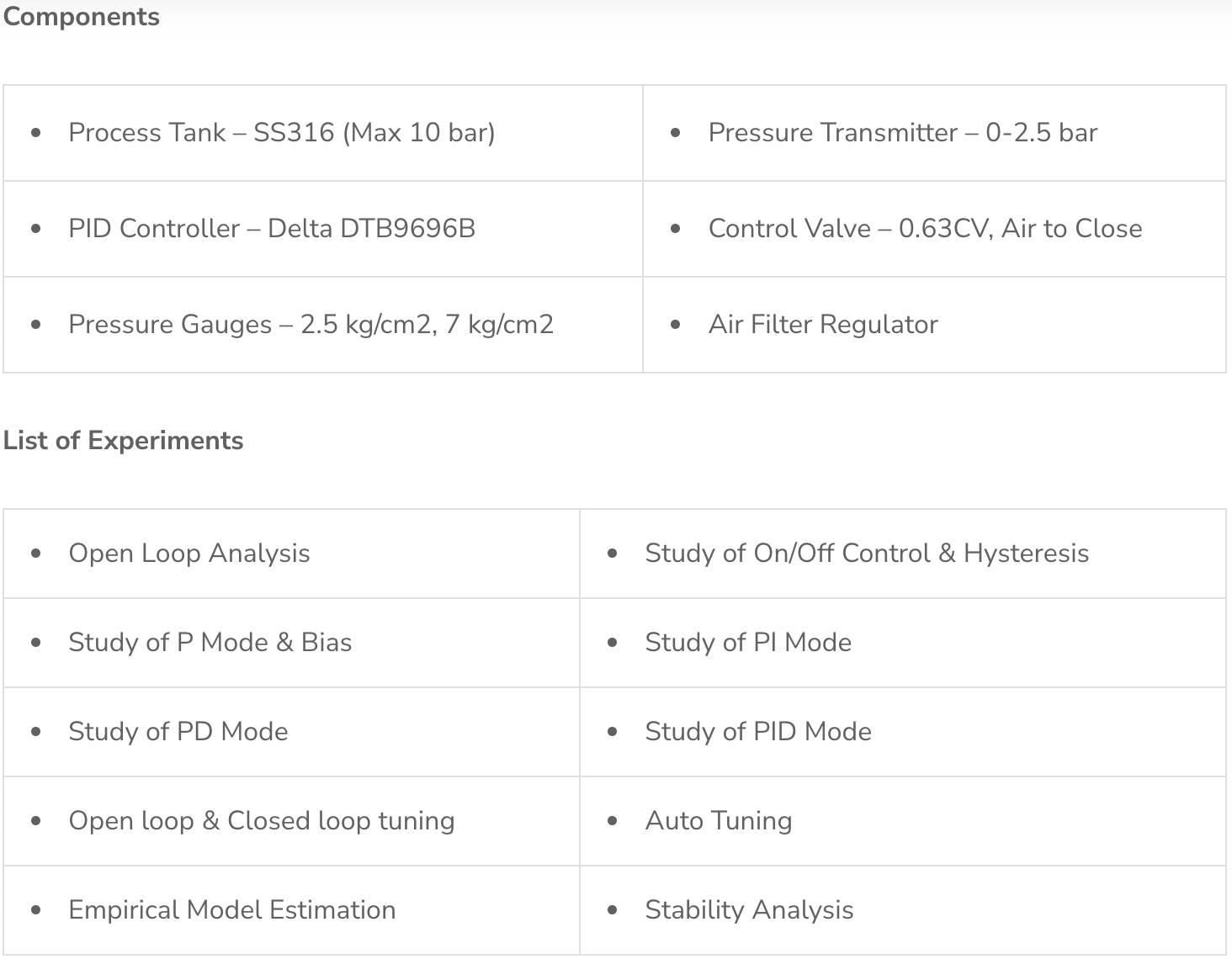