Continuous Stirred Tank Reactor (CSTR) Trainer
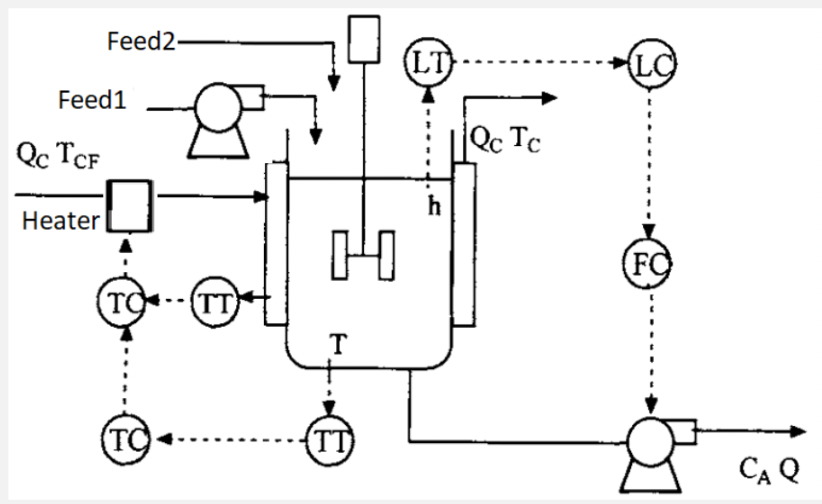
Description
The setup is designed to demonstrate principles of CSTR arrangement. It consists of two feed tanks and feed pumps. The flow to the reactor and the out flow from the reactor can be controlled by controlling the speed of the pumps. The reactor with jacket arrangement is made of high-quality stainless steel for durability and long life and equipped with stirrer driven by an electric motor. The speed of the stirrer can also be controlled. A heater setup is used to provide hot water to the jacket. The heater temperature can be controlled using a SSR and RTD arrangement. All the components are designed to hope up industrial standard. The process parameter is controlled by a PLC Unit using Modbus communication. These units along with necessary piping are fitted on the support frame. The setup is designed for tabletop placement and access. The controller is connected to computer through USB for monitoring and controlling the process. User friendly software will be supplied along with the hardware to perform different set of experiments. The typical P&I diagram is shown below.
Features
- Anodized aluminum frames
- Industrial standard components
- Tabletop structure
- Corrosive resistive SS materials
- Durable CPVC piping for hot line
- Configurable control using patch cords
- Powder coated MS panel
- Interface with LabVIEW / Matlab
- Modbus Communication
- Single click data log, export features
Range of Experiments
- Single Loop Control Experiments (Level / Flow / Temperature)
- Measurement and transmitter characteristics study
- Empirical Model Estimation
- Study of Open loop characteristics
- Study of On/Off Control & Hysteresis
- Study of P Mode Control & Bias
- Study of PI Mode Control
- Study of PD Mode Control
- Study of PID Mode Control
- Open loop & Closed loop PID tuning
- Stability analysis
- Advanced Control Experiments
- Temperature + Temperature Cascade
Control
Level + Flow Cascade Control
Feedforward + Feedback Control
Ratio Control
Gain scheduling Control
Over Ride Control
Internal Model Control (IMC)
Second and Higher order Empirical
Model Estimation
Fuzzy Logic Controller Design & Control
Split range control
- Temperature + Temperature Cascade
Requirements
• Water Supply 2 LPM at 5 m head
• Drain
• Electricity Supply: 1Phase, 220 V AC, 3 kW
• Required Chemicals
Product Specifications
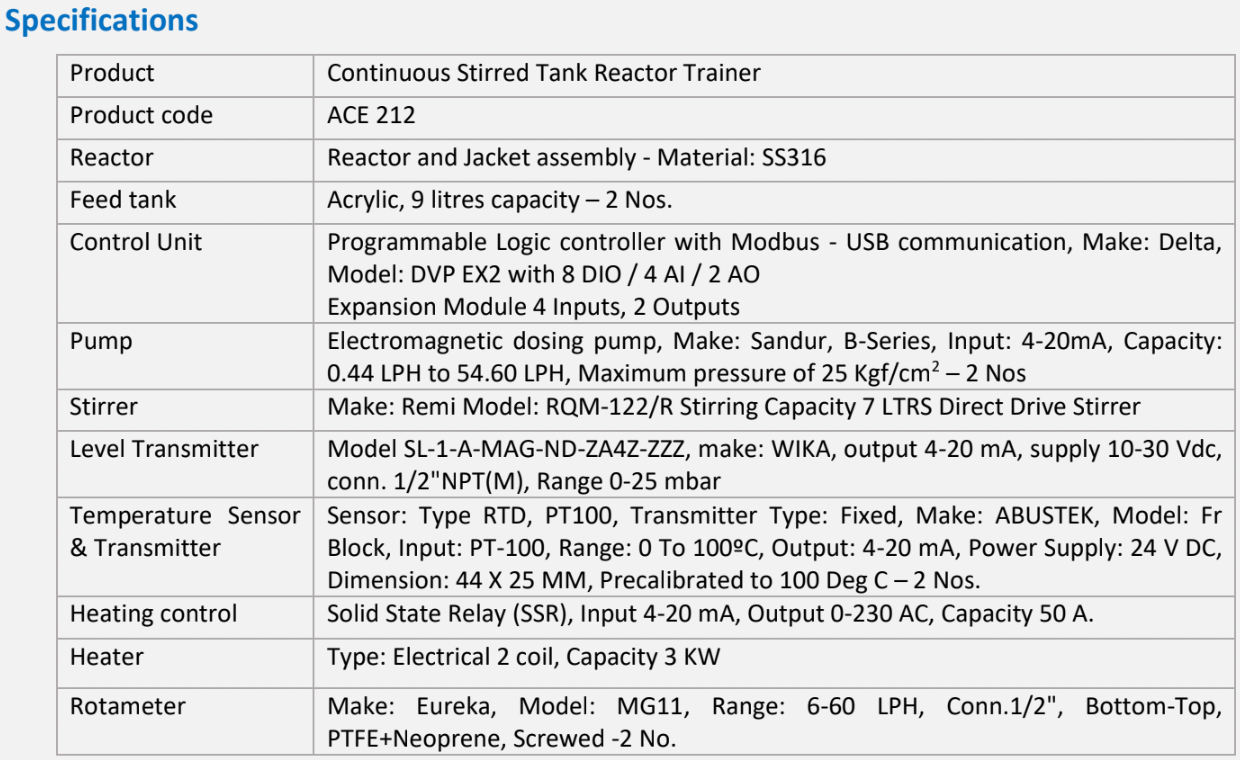